Researchers on the 4th Physics Institute on the College of Stuttgart have demonstrated the viability of 3D printed polymer-based micro-optics in a demanding laser surroundings.
Detailed within the Optics Journal, the examine outlines using 3D printing know-how to straight manufacture microscale optics onto optical fibers, seamlessly integrating fibers and laser crystals right into a single laser oscillator. Sustaining stability, the ensuing hybrid laser produces a constant output exceeding 20 mW at 1063.4 nm, reaching a peak of 37 mW. What units this laser aside is its mixture of the compactness, sturdiness, and cost-effectiveness of fiber-based lasers together with the versatile properties of crystal-based solid-state lasers, together with numerous powers and colours. This analysis represents a big development in direction of creating reasonably priced, small, and dependable lasers, notably useful for lidar methods in autonomous autos.
“We considerably lowered the scale of a laser by utilizing 3D printing to manufacture high-quality micro-optics straight on glass fibers used within lasers,” mentioned analysis group chief Simon Angstenberger, 4th Physics Institute on the College of Stuttgart. “That is the primary implementation of such 3D printed optics in a real-world laser, highlighting their excessive injury threshold and stability.”
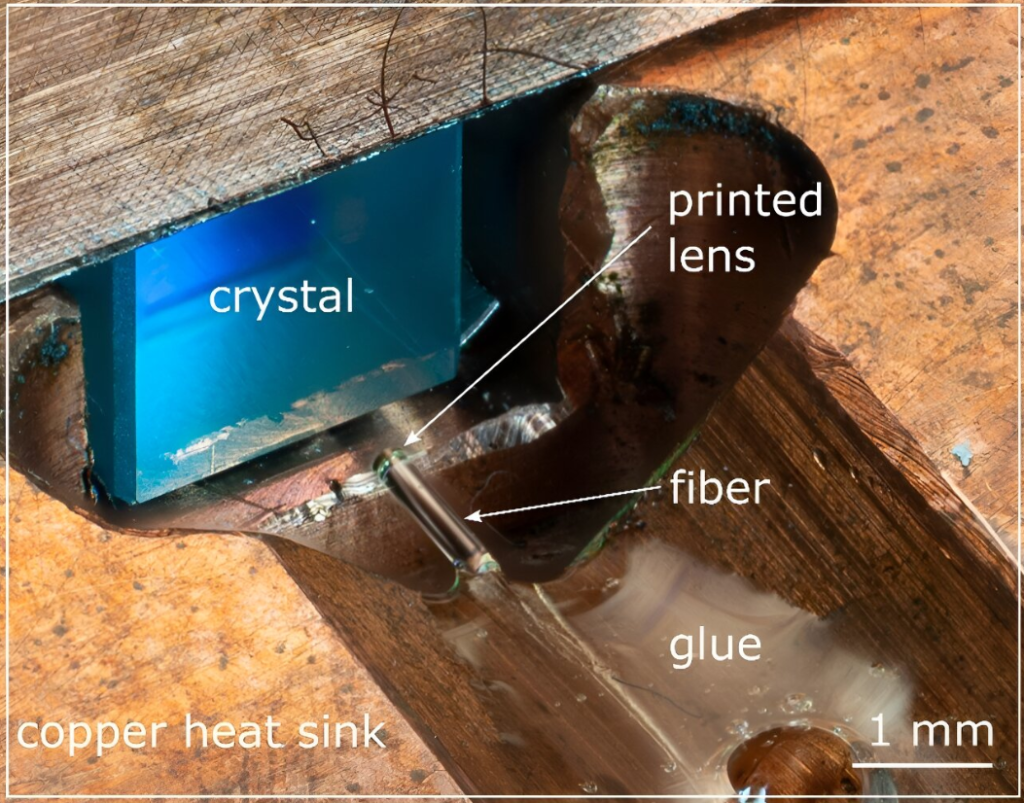
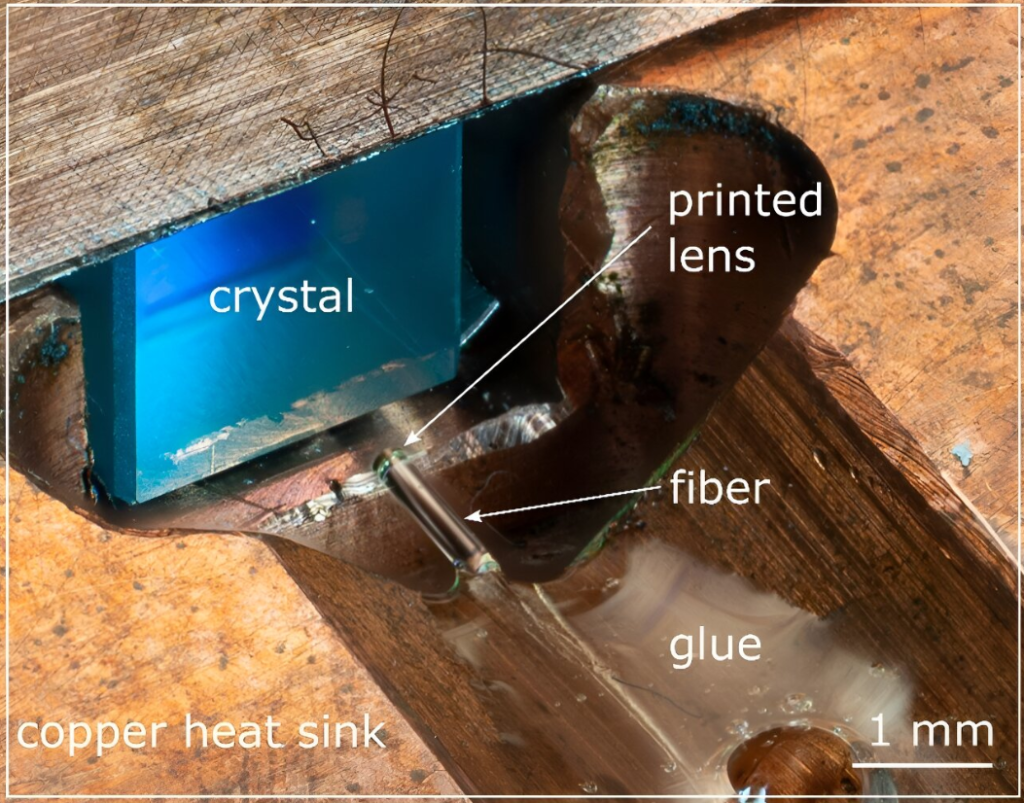
From cumbersome lasers to compact powerhouses with 3D printed optics
The 4th Physics Institute on the College of Stuttgart has been actively concerned in advancing 3D printed micro-optics, notably within the space of printing straight onto fibers. Utilizing the two-photon polymerization 3D printing strategy, the researchers achieved the creation of miniaturized optics with excessive precision and launched novel functionalities similar to free-form optics and complicated lens methods.
On this examine, a Nanoscribe 3D printer was used to create lenses measuring 0.25 mm in diameter and 80 microns in peak straight onto a fiber of matching dimensions by means of two-photon polymerization. The process included designing an optical component utilizing industrial software program, inserting the fiber into the 3D printer, and executing the printing of the advanced construction onto the fiber’s finish. Precision in aligning the printing with the fiber and guaranteeing accuracy within the printing course of had been essential elements of this meticulous process.
After printing, the researchers assembled the laser and its cavity, choosing fibers as an alternative of conventional mirrors. This strategy resulted in a hybrid fiber-crystal laser, with the printed lenses focusing and gathering gentle into and out of the laser crystal. The fibers had been then secured in a mount to reinforce system stability and scale back susceptibility to air turbulence, leading to a compact 5 x 5 cm2 laser system.
Over a number of hours, the laser energy underwent steady monitoring, confirming that the printed optics exhibited no deterioration and didn’t adversely have an effect on the long-term properties of the laser. Scanning electron microscopy photos of the optics post-use within the laser cavity revealed no seen injury. The researchers are at the moment specializing in optimizing the effectivity of the printed optics, exploring bigger fibers and totally different lens designs to reinforce output energy and customization choices for particular functions.
“Till now, 3D printed optics have primarily been used for low-power functions similar to endoscopy,” mentioned Angstenberger. “The power to make use of them with high-power functions may very well be helpful for lithography and laser marking, for instance. We confirmed that these 3D micro-optics printed onto fibers can be utilized to focus giant quantities of sunshine all the way down to a single level, which may very well be helpful for medical functions similar to exactly destroying cancerous tissue.”
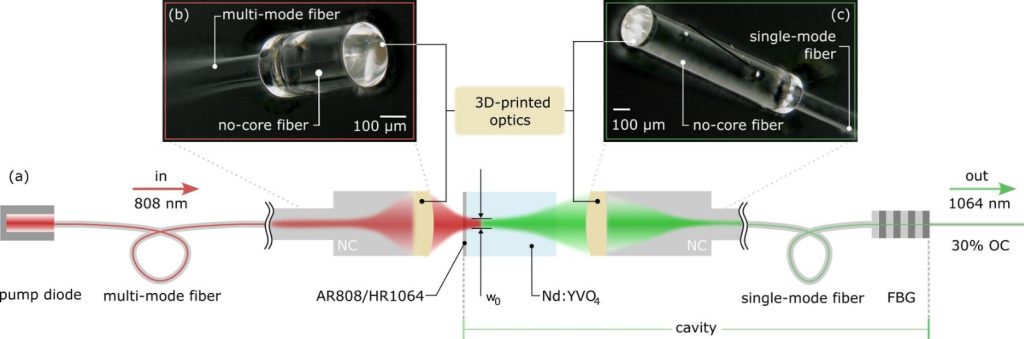
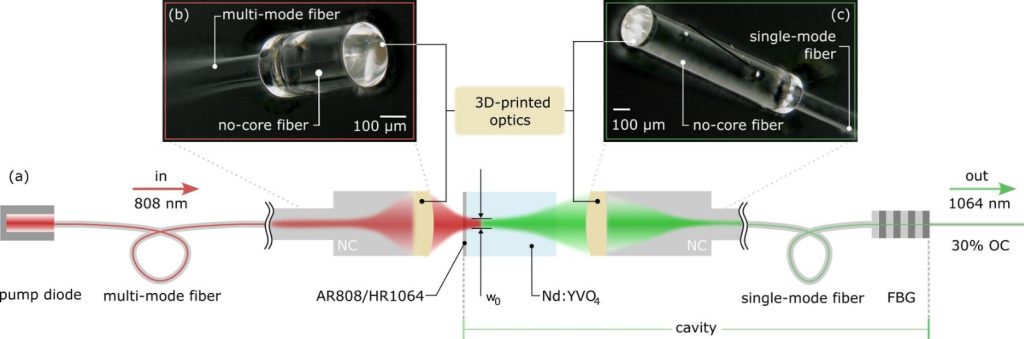
Developments in laser know-how
In an interview with 3D Printing Trade, Head of L-PBF at Fraunhofer IAPT, Philipp Kohlwes, shared insights into the institute’s beam shaping analysis for enhancing stability and productiveness in metallic 3D printing. The analysis centered on adapting laser profiles to optimize meltpool power enter in laser powder mattress fusion (LPBF), addressing points brought on by conventional Gaussian profiles. Important for laser profile adjustment, beam shaping ensures a uniform temperature distribution. The know-how yields benefits like enhanced microstructure management, potential price financial savings, and as much as 2.5 occasions sooner printing, contributing to elevated productiveness.
Final yr in January, 3DM Digital Manufacturing unveiled a know-how enabling customers to customise their Selective Laser Sintering (SLS) 3D printing laser for particular supplies or functions. Utilizing Quantum Cascade Lasers, the corporate’s proprietary laser provides adjustable wavelengths, sooner laser absorption, and excessive floor end. With functions in polymer manufacturing, the scalable know-how goals to increase industrial 3D printing’s market share.
Learn all of the 3D Printing Trade protection from Formnext 2023.
What does the way forward for 3D printing for the following ten years maintain?
What engineering challenges will must be tackled within the additive manufacturing sector within the coming decade?
To remain updated with the most recent 3D printing information, don’t overlook to subscribe to the 3D Printing Trade e-newsletter or comply with us on Twitter, or like our web page on Fb.
When you’re right here, why not subscribe to our Youtube channel? That includes dialogue, debriefs, video shorts, and webinar replays.
Are you in search of a job within the additive manufacturing business? Go to 3D Printing Jobs for a collection of roles within the business.
Featured picture reveals researchers printed microscale lenses straight onto optical fibers, permitting them to compactly mix fibers and laser crystals inside a single laser oscillator. Picture by way of Moritz Floess and Simon Angstenberger, 4th Physics Institute at College of Stuttgart in Germany.