AMAZEMET, a Warsaw-based firm, is getting ready to launch its Powder2Powder (P2P) atomization system on the Formnext 2024 occasion. Designed for the additive manufacturing (AM) trade, the P2P system affords a streamlined strategy to recycling metallic powders and producing tailor-made pre-alloy powders instantly from powder feedstock.
The P2P system combines plasma processing with ultrasonic atomization to transform irregular or outsized particles into extremely spherical, satellite-free powders optimized for AM functions. This course of (see Determine 1) permits powder measurement to be managed independently from the preliminary feedstock’s traits. The P2P know-how, uniquely, facilitates the direct atomization of pulverized titanium (Ti) feedstock, making it a particular resolution in metallic powder manufacturing.
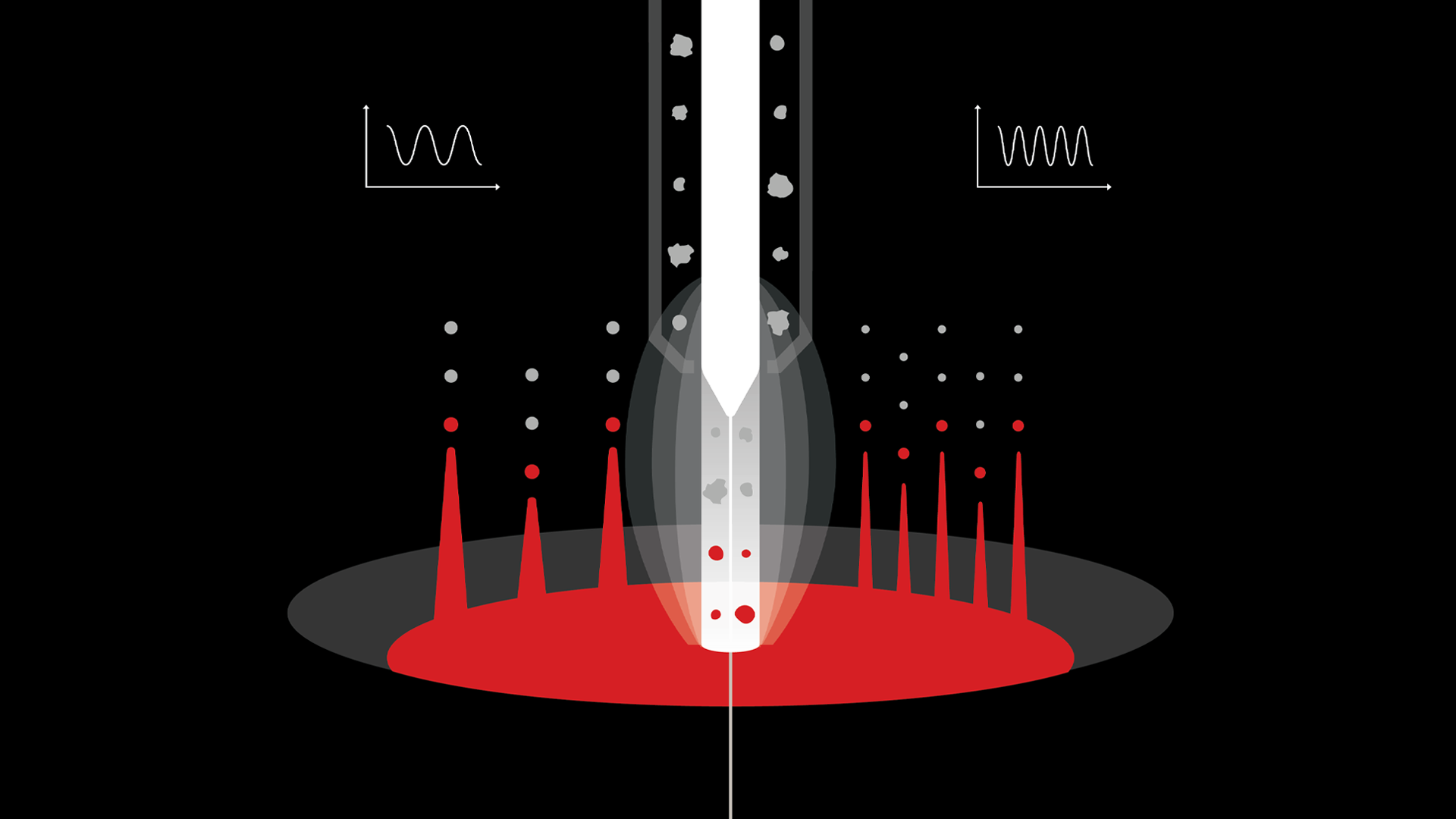
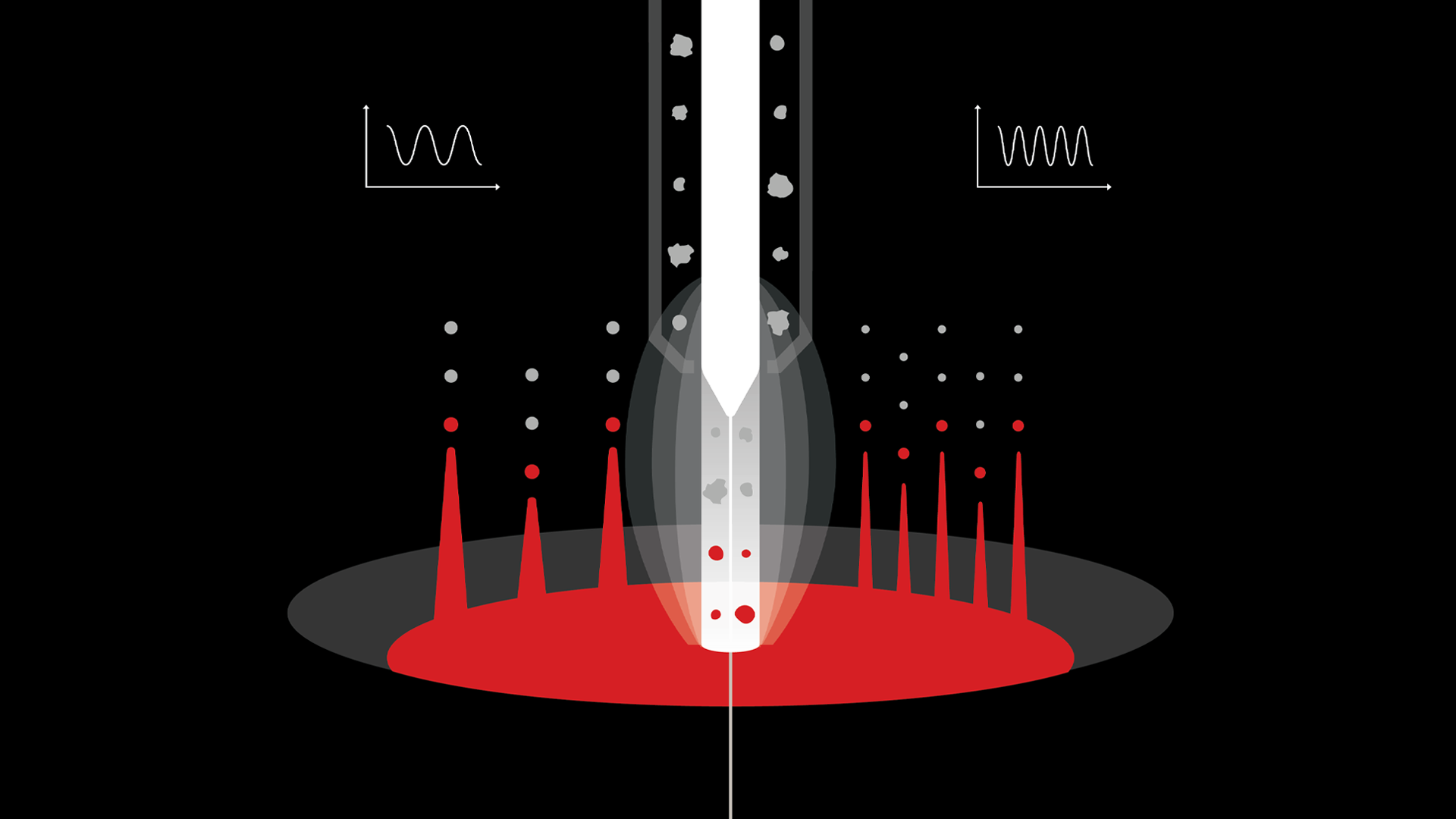
Efficiency and Effectivity in Testing
AMAZEMET carried out intensive testing on +200 μm outsized and irregular titanium alloy powders, demonstrating the system’s capabilities. Working at 40 kHz, the P2P system achieved a powder morphology with a side ratio (D50) exceeding 0.95, and managed particle measurement distribution (PSD) with a D90 < 80 μm. The checks resulted in powder particles <63 μm at a powerful yield of over 80%, with almost 97% of the ensuing powder being appropriate for AM strategies, equivalent to Laser Powder Mattress Fusion (LPBF), Directed Power Deposition (DED), and Electron Beam Melting (EBM). This effectivity highlights the system’s potential to help sustainable powder manufacturing by optimizing the usage of feedstock.
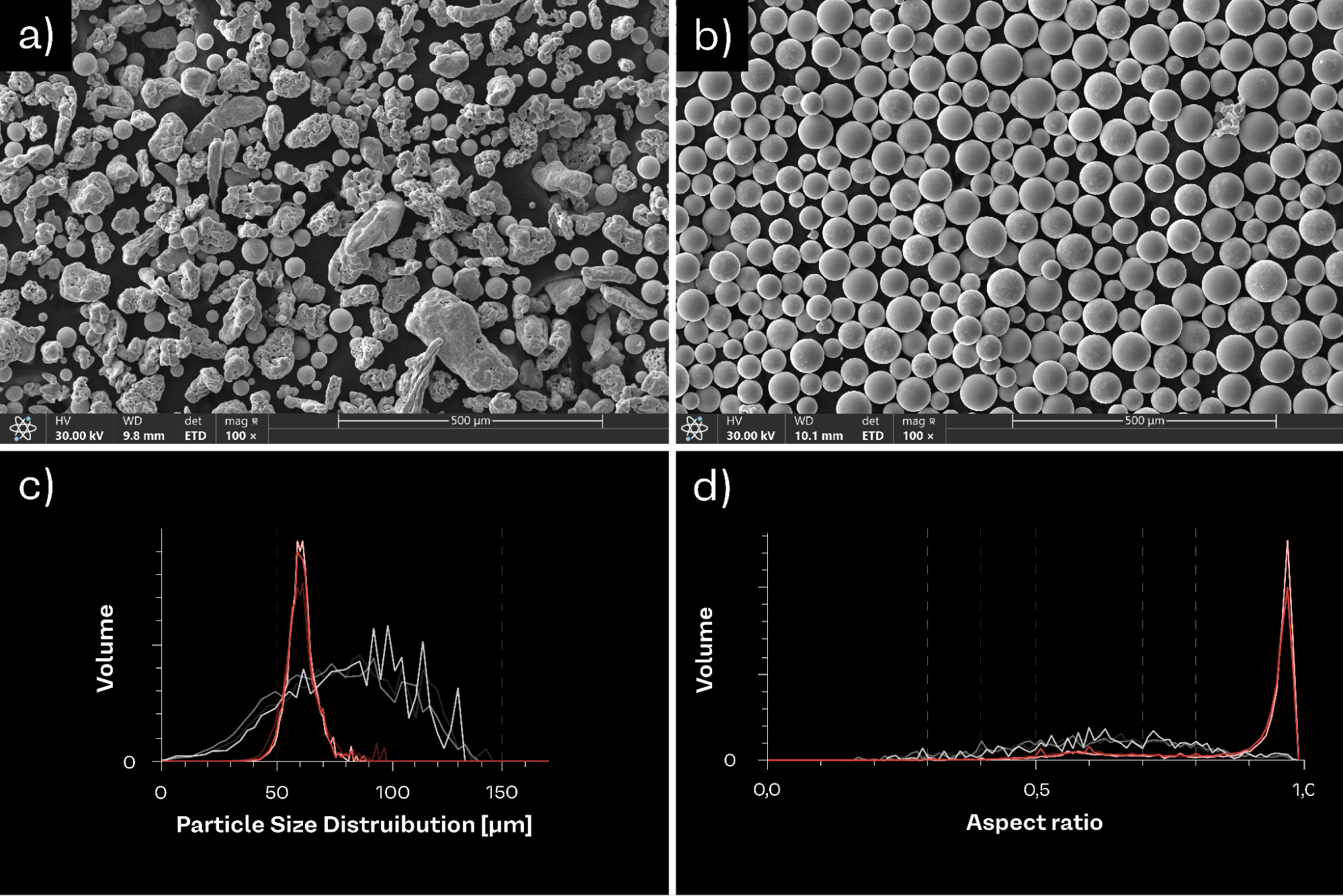
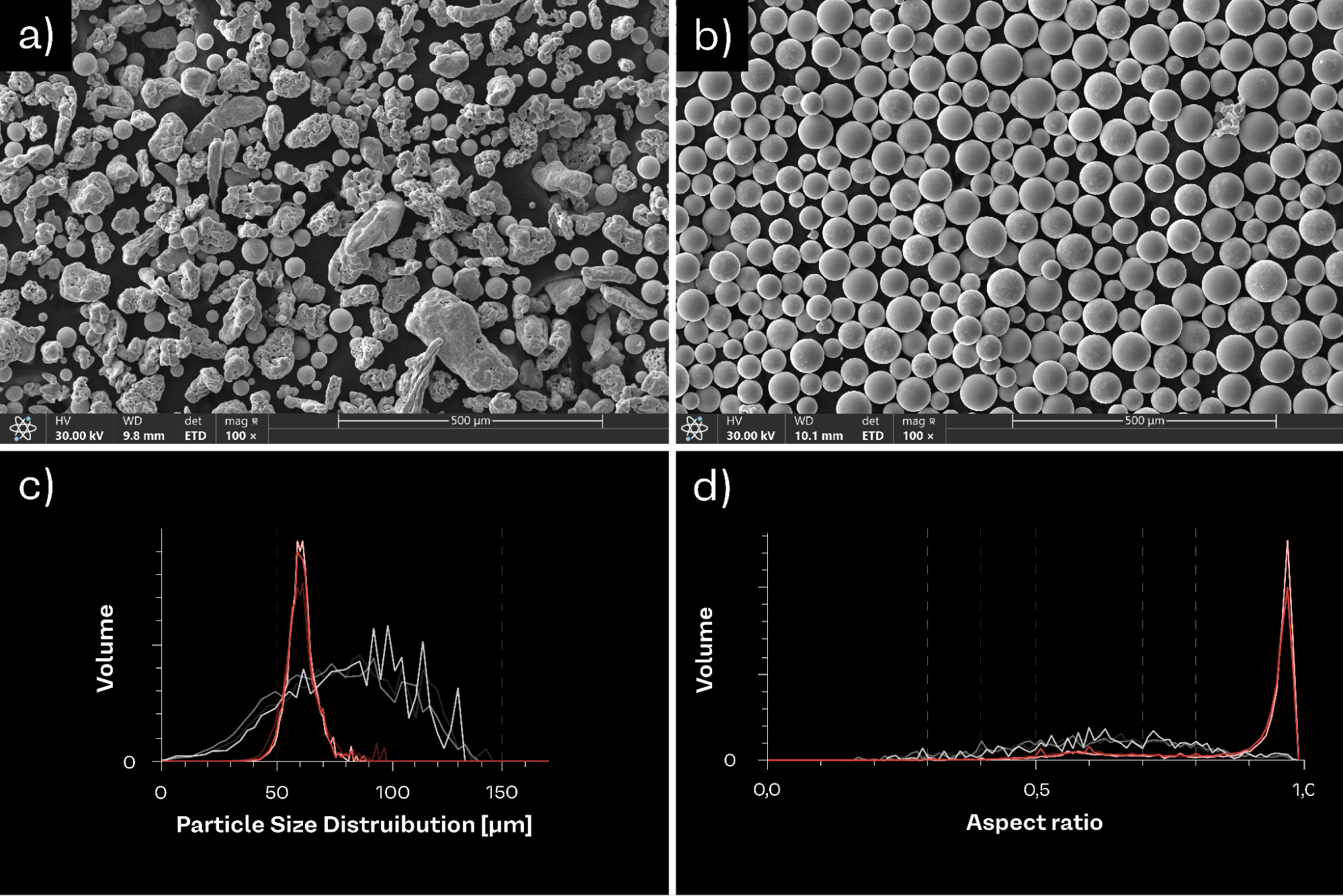
Along with recycling, the P2P system can course of combos of elemental powders to create pre-alloyed supplies with particular chemical compositions. This functionality serves each analysis and industrial functions, enabling tailor-made materials manufacturing. AMAZEMET’s trials with a Ti and 10% wt. Mo mix confirmed profitable alloying, with each refractory parts forming homogeneous powders. This patented know-how, scheduled for launch in early 2025, instantly addresses AM trade challenges of upcycling powder waste and creating customized powders, offering superior performance in comparison with conventional recycling strategies.
Key Options of the Powder2Powder System
- Particle Dimension Distribution Management
The system adjusts PSD, reworking outsized and undersized particles into AM-compatible powder optimized for LPBF, DED, and comparable applied sciences. - Powder Morphology
Combining plasma know-how with ultrasonic atomization, the system converts irregular powders into spherical, satellite-free particles that enhance efficiency in AM processes. - Powder Alloying
Elemental powder blends or industrial alloys with minor additions could be instantly atomized with out preprocessing steps. Not like different atomization processes, equivalent to EIGA or plasma atomization, new alloys could be developed quickly with out electrode casting or wire drawing. - Multi-Materials Functionality
The P2P system handles a various vary of metallic powders, together with metal, titanium, nickel, refractory alloys, and high-entropy alloys (HEAs), enabling manufacturing of powders for varied AM functions. - Sustainability and Effectivity
By changing unusable powders into AM-ready materials, the system reduces waste and promotes sustainable manufacturing practices.
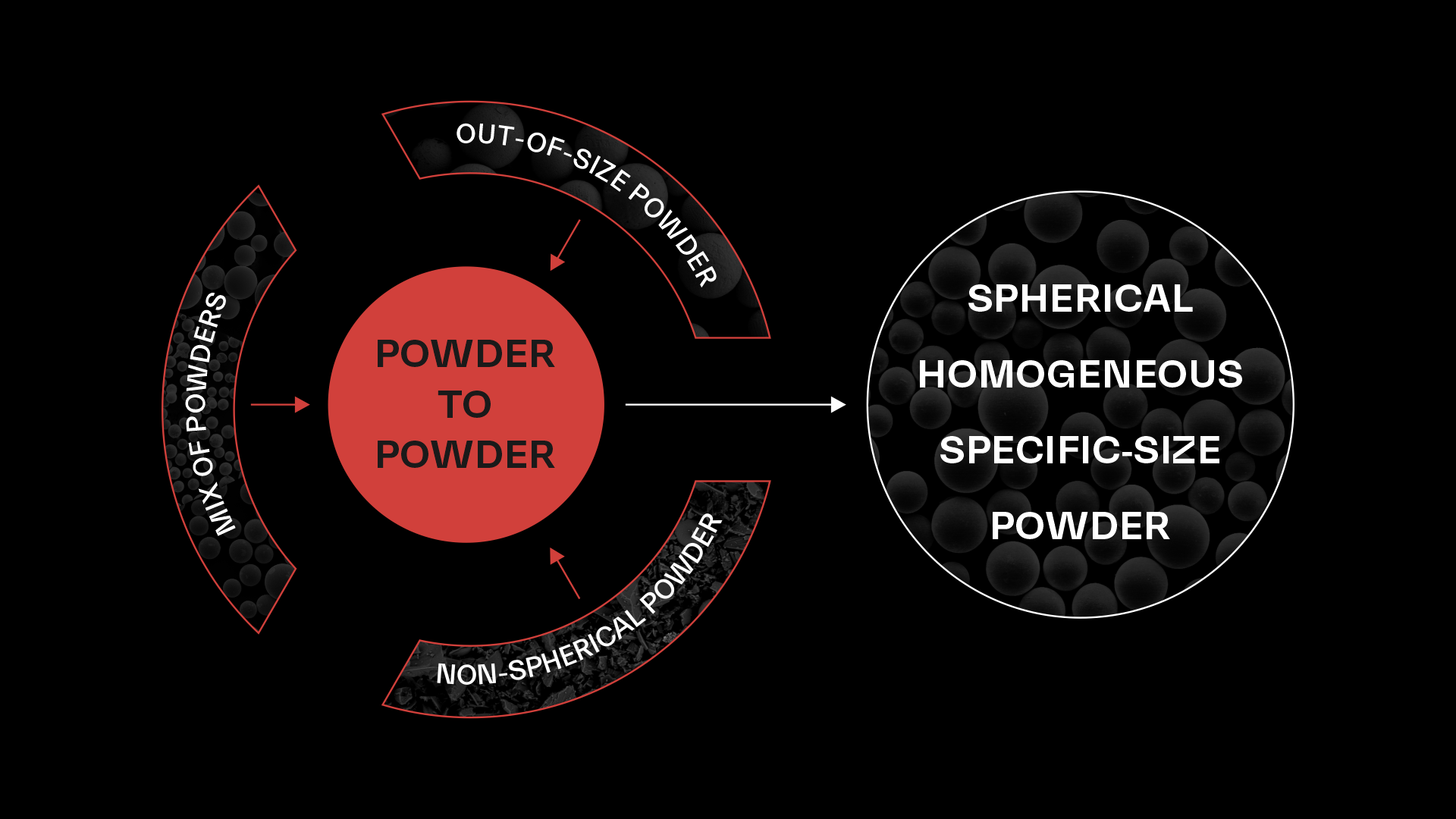
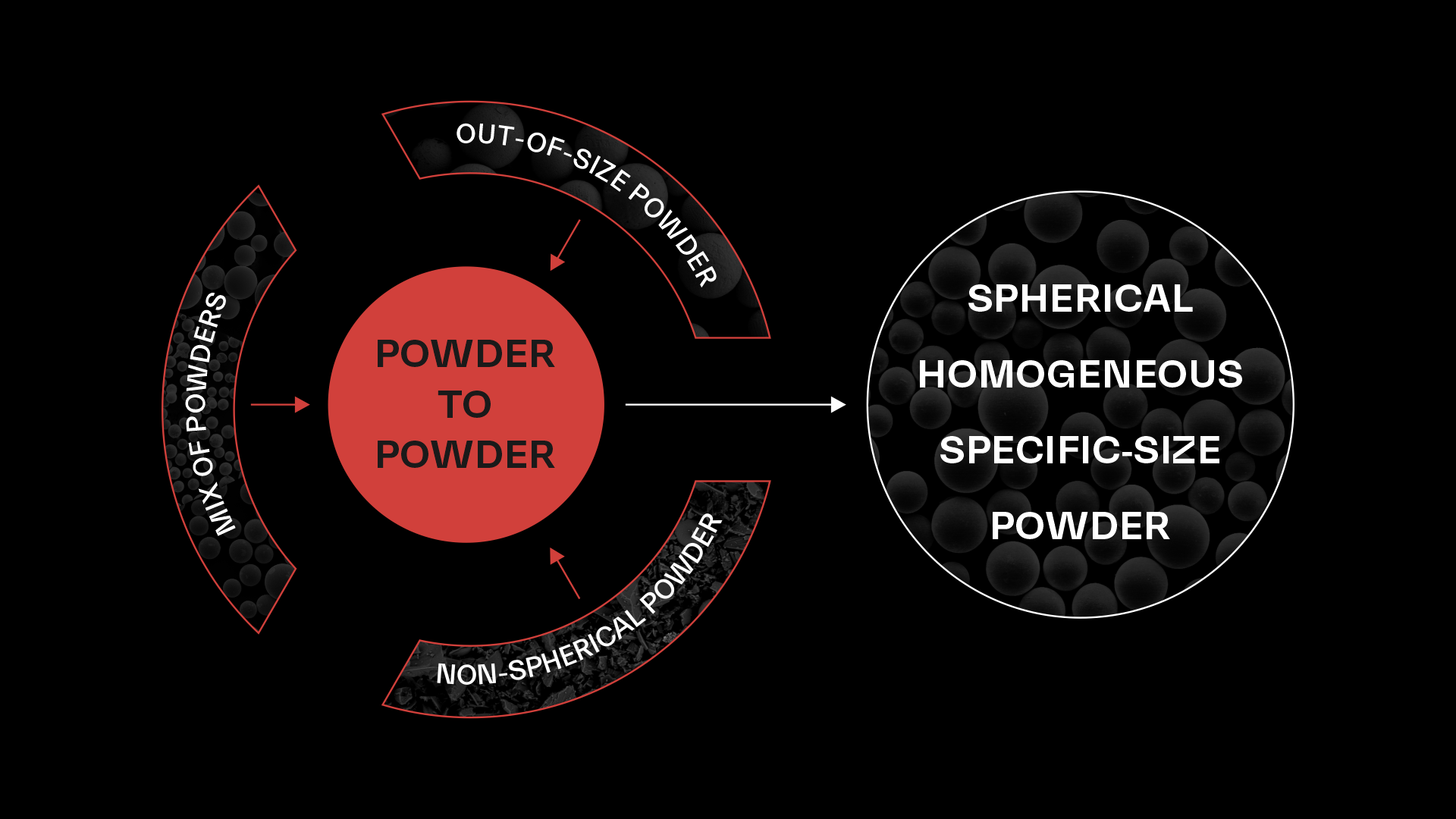
Assertion from AMAZEMET’s CEO
Łukasz Żrodowski, the inventor and CEO of AMAZEMET, describes the P2P system’s distinctive strategy: “The Powder2Powder system goes past recycling. It provides producers the flexibility to customise powder compositions, enhance powder sphericity, and optimize particle measurement distribution, fixing essential points within the AM trade. We’re excited to debut this at Formnext 2024, the place we’ll showcase the way it can improve the effectivity and sustainability of powder-based manufacturing.”
Formnext 2024 attendees can have the primary alternative to see this know-how in motion. The P2P system offers an all-in-one resolution for recycling and customized alloy powder manufacturing, providing producers a brand new software for additive manufacturing. Extra data on the Powder2Powder system can be obtainable at p2p.amazemet.com.
Go to AMAZEMET at FORMNEXT 2024 – Corridor 12.0, E61, see the interactive floorplan.